MSE, BME students work collaboratively with CWRU's nanojet printer
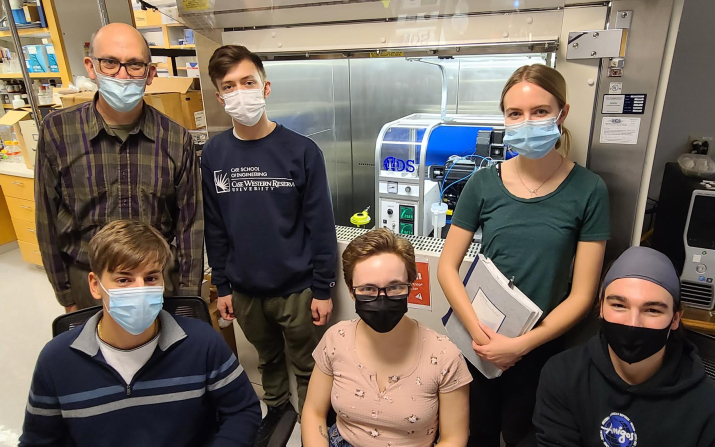
Janet Gbur has always been a believer in introducing undergraduate engineering students to a wide variety of materials testing and characterization techniques before they graduate. “Participation in research provides an opportunity for students to connect the classroom theory to real-world applications as well as develop key skill sets that can be valuable to future internships, graduate school, or their career.” said Gbur, a senior research associate in Case Western Reserve University’s Department of Materials Science and Engineering.
Gbur, who was a baton twirling coach for 30 years, considers herself a “coach of the next generation of engineers.” She and Doug Shire, a research health scientist at the VA Northeast Ohio Healthcare System, are currently working on four projects involving the NanoJet Aerosol Printer housed in CWRU’s Additive Manufacturing for Biotechnology Core, on which Gbur is putting her skills as an engineering coach to use.
The projects focus on developing aerosol printed, flexible circuits for use in medical applications. Gbur and Shire have assembled what Gbur described as an “amazing” team of students. Two seniors from CWRU’s Department of Materials Science and Engineering, Paco Sheeran and Hayley Wagreich, have joined the team to complete their senior projects. Sylvie Crowell, a junior in the Department of Materials Science and Engineering, has been researching with Gbur since her freshman year. Juan Garcia, a junior in CWRU’s Department of Biomedical Engineering, worked with Gbur in 2021 as a Wen H. Ko summer intern and is continuing to research with her. Mitchell Melander, also a biomedical engineering student, reached out to Gbur after hearing about her research at the Cleveland VA Medical Center’s Advanced Platform Technology Center. “I love seeing materials students and biomedical engineering students working together,” said Gbur. “When you have students who are interested and intellectually curious, these are the perfect people to get involved.”
"At its most basic level, the students have some time that they can invest in trying out different combinations of parameters and settings that are just very time consuming,” said Shire. “At the same time, the students are learning about the additive manufacturing process and everything that goes into making the parts for their projects.” He described the project as a win-win because the students are learning and also helping to move the VA research forward. Shire is working with Sheeran on building a wirelessly monitored sensor to go on a pair of gloves that someone would wear. This sensor would allow a measurement of force that could be used to help teach someone how to do a task. “It’s hard to describe in words how tightly you need to grip something,” said Shire. “These sensors are often purchased and glued onto things; the idea here is to make the sensor part of the glove instead of having to purchase the sensors separately. The printer is well suited to that task and is capable of printing on uneven surfaces.”
Having wanted to learn more about additive manufacturing and electronic printing for his senior project, Sheeran has appreciated collecting data, creating effective testing procedures and learning about which materials serve as effective substrates. “This project is about understanding a lot of different parameters that all affect how prints turn out and trying to tackle some of them has taken a lot of different prints and analysis,” he said of his efforts to develop the best ink and substrate combination for the sensorized glove. Additionally, he has focused on using optical profilometry, optical microscopy, and scanning electron microscopy for characterization of the printed traces.
Crowell and Garcia’s projects relate to optimizing the printer for different applications and use. Both have worked on mechanical and electrical characterization of the wire-based leads, while Garcia is also focused on developing the printed circuitry and evaluating the long-term reliability of the implanted system. Wagreich is performing studies of the printer's long term stability and the reproducibility of the printer's traces.
Additionally, the group hopes to develop fabrication techniques to replace the current wire-based implantable leads system with aerosol-printed, flexible leads by focusing on mechanical characterization of the potential substrates, circuit design, printing optimization, and characterization of the printed traces. Crowell has used atomic force microscopy and scanning electron microscopy to study mechanical characterization and Melander is developing techniques for the mechanical characterization of the substrates and final printed devices.
"It’s one thing to have a student who wants to volunteer, but it also takes a mentor who is enthusiastic about helping the students, and (Gbur) is really exceptional at that,” said Shire.
Gbur first met Shire in 2019 through Dustin Tyler, Kent H. Smith Professor of Biomedical Engineering at Case Western Reserve University, when working on a project focused on implantable systems to restore the sense of touch in amputees. They have been researching together ever since, though this is their first joint project working with students.