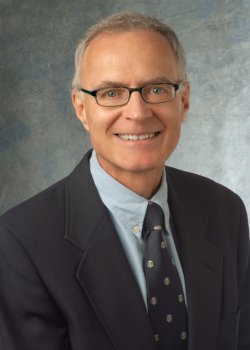
AMMRC Celebrates 35 years of Mechanical Characterization at CWRU
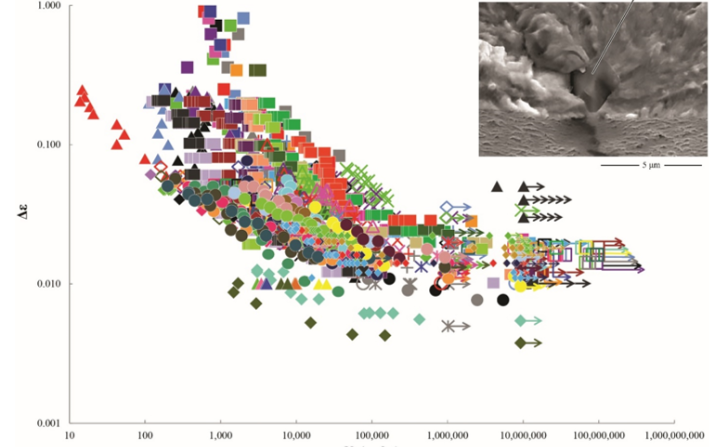
The years 2015-2020 continued work from the late 2010’s with new funding exceeding $8M, along with continued growth of the AMMRC manufacturing facilities and Lewandowski research group to include: Kevin Macke (M.S.), Tiffany Dux (M.S.), Beth Andrasik (M.S.), Daniel Young (M.S.), Erica Bindas (M.S.), Conrad Park (M.S.), Zeesha Braslawsce (M.S.), Ji Xia (M.S.), Sarah Heyse (M.S.), Henry Neilson (M.S./Ph.D.), Matt Dahar (M.S./Ph.D.), Wenbin Gao (Ph.D.), Ben Palmer (M.S./Ph.D.), Austin Ngo (M.S./Ph.D.), Mohsen Seifi (M.S./Ph.D./Research Associate), Janet Gbur (Ph.D./Research Associate), Dr. Hongwang Yang, and Dr. Jiao Luo. Rich Tomazin provided expanded AMMRC staff help in this era with the retirement of Chris Tuma.
Multiple new individual and collaborative multi-year research grants were obtained from Lincoln Electric, Office of Naval Research (ONR), Naval Air Systems Command (NAVAIR), General Electric, SPR Therapeutics, Defense Advanced Research Projects Administration (DARPA)/National Institute of Health (NIH), Department of Energy (DoE), Veterans Administration (VA), Los Alamos National Lab (LANL), Air Force Research Lab (AFRL), and America Makes. In addition, the American Lightweight Materials Manufacturing Innovation Institute (ALMMI), also known as Lightweight Innovations for Tomorrow (LIFT), awarded $686K to CWRU over two grants to investigate process/property relationships in novel nano-metal matrix composites produced by powder metallurgy as well as friction stir processing of these materials. A variety of industrially relevant projects were conducted in close collaboration with the companies and agencies listed, as summarized below.
This era continued to expand work on the evaluation of the mechanical reliability of implantable electrodes in collaboration with The Cleveland Functional Electrical Stimulation (FES) Center under the leadership of then Director, Professor P. Hunter Peckham. A major review article on ‘Fatigue and Fracture of Wires and Cables for Biomedical Applications’ was published by Drs. Gbur and Lewandowski in International Materials Reviews. In addition, the AMMRC continued extensive work examining the microstructure and mechanical reliability of additively manufactured materials, including Ti-6Al-4V, CP-Ti Grade 2, AlSi10Mg, GRCop, IN718, 17-4 PH Stainless Steel, Ti-48Al-2Nb-2Cr processed via powder bed fusion as well as wire-based techniques. In particular, the effects of systematic changes in processing conditions and process-induced defects on fracture-critical properties including toughness and fatigue were determined. A major invited review article ‘Metal Additive Manufacturing: A Review of Mechanical Properties’ was prepared by Drs. Lewandowski and Seifi for Annual Reviews of Materials Research to capture work that had been conducted to date as well as provide recommendations for future research. Additional papers discussed issues related to Qualification and Certification of additive manufacturing (AM) processes and parts. [JOM, 68, 747–764 (2016), JOM, 69, 439–455 (2017)]
Figure 1 shows the variation in fatigue life of NiTi biomedical wires along with a scanning electron microscopy (SEM) fractograph illustrating critical fatigue initiating features responsible for reduced fatigue life as well as scatter in fatigue lives. Important work continues on examining the effects of increased alloy cleanliness on the fatigue performance and mechanical reliability of these materials as well as other biomedically-relevant materials and structures.
Figure 1. Strain-Cycles to Failure (S-N) plot showing the effects of changes in strain level on cyclic fatigue behavior of NiTi biomedical wires. The SEM image shows a typical fatigue initiating feature responsible for reduced fatigue lives and scatter in the fatigue data. [reference - International Materials Reviews, 61:4, 231-314 (2016)]
Figure 2 summarizes the important effects of processing techniques, process-induced defects, and surface roughness on the Stress-Cycles (S-N) fatigue behavior of Ti-6Al-4V. As-deposited surfaces shown in Figure 3 produce significant debits to the fatigue characteristics. Additional work is being conducted to examine the effects of processing and surface conditions on the fatigue reliability of AM-processed materials.
Figure 2. Stress-Cycles to Failure (S-N) plot showing the effects of changes in stress level and AM processing conditions (e.g. as-deposited, machined, Hot-Isostatic Pressed, etc.) on the S-N fatigue behavior of Ti-6Al-4V. [reference – Annual Review of Materials Research, 46, 151-186 (2016)].
Figure 3. SEM image of as-deposited surface of AM-processed Ti-6Al-4V. Partially melted powders and other features (i.e. surface roughness, cracks) are evident at various locations. [reference - JOM, 67(3), 597–607 (2015)]. These have been shown to produce severe debits to the S-N fatigue behavior of AM-processed materials, as shown in Figure 2.
We invite you to join us in the AMMRC’s 35th anniversary celebration as we celebrate decades of research, development, and Center milestones. Visit the AMMRC web site, ammrc.case.edu, and keep watch on social medial for insights on the AMMRC through the decades as we share stories about the evolving laboratory and honor the efforts of the diverse academics, staff, and students that have propelled the AMMRC forward.
Social media: Join us on social media for fun and engaging content that will help you discover the AMMRC’s history and where it’s heading in the future. #AMMRC35.