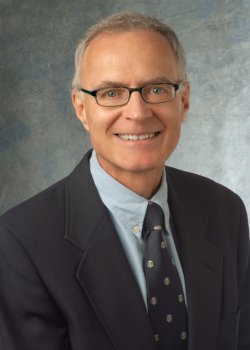
AMMRC Celebrates 35 years of Mechanical Characterization at CWRU
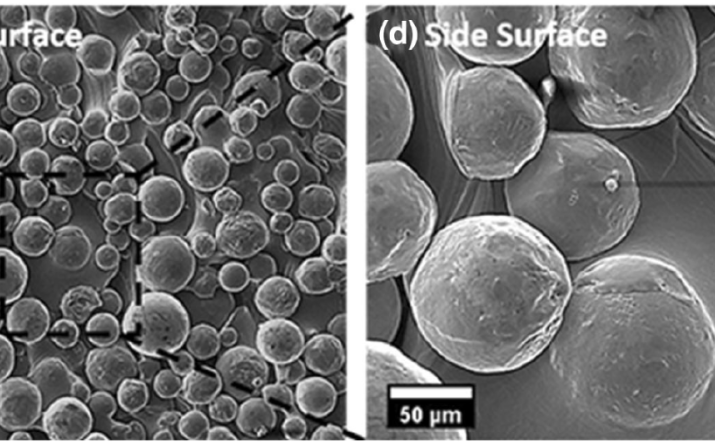
The years 2010-2015 continued work from the late 2000’s with new funding exceeding $5M, along with continued growth of the AMMRC manufacturing facilities and Lewandowski research group to include: Kyle Kulpinski (M.S.), Jessie Booth-Clinton (M.S.), John Bobanga (M.S.), Kevin Macke (M.S.), Tiffany Dux (M.S.), Beth Andrasik (M.S.), Mohsen Seifi (M.S/Ph.D.), Janet Gbur (Ph.D.), Henry Neilson (M.S./Ph.D.), Matt Dahar (M.S./Ph.D.), Chun-Kuo Huang (Ph.D.), Lisa Deibler (Ph.D.), Hossein Lavvafi (Ph.D.), George Sunny (Ph.D.), Dr. Ravi Varadarajan, Dr. Jun Yi, Dr. Bin Sun, Dr. Adel El-Shabasy, Dr. Hala Hassan, Dr. Hala Hassan Salman. Rich Tomazin also began to provide AMMRC staff help in this era.
Multiple new individual and collaborative multi-year research grants were obtained from Defense Threat Reduction Agency (DTRA), Lincoln-Electric, Army Research Office (ARO), Office of Naval Research (ONR), Naval Air Systems Command (NAVAIR), General Electric, National Institute of Health (NIH), Carleton Technologies, Luxfer USA, Department of Energy (DoE), Veterans Administration (VA), Los Alamos National Lab (LANL), In addition, the National Additive Manufacturing Innovation Institute (NAMII), now known as America Makes, awarded $1.1M to a multi-institution team led by CWRU to begin to investigate ‘Rapid Qualification Methods for Powder Bed Direct Metal AM Processes’. A variety of industrially relevant projects were conducted in close collaboration with the companies and agencies listed, as summarized below.
In addition to this era continuing to expand work on the evaluation of the mechanical reliability of implantable electrodes in collaboration with The Cleveland Functional Electrical Stimulation (FES) Center under the leadership of then Director, Professor P. Hunter Peckham. The AMMRC/CWRU received one of the first funded projects from the recently established NAMII, now known as America Makes, on Additive Manufacturing of metals for structural applications. The AMMRC led the microstructure and mechanical reliability evaluations of additively manufactured Ti-6Al-4V processed via both laser- and electron beam powder bed fusion. In particular, the effects of systematic changes in processing conditions and process-induced defects on fracture-critical properties including toughness and fatigue were determined. Computerized tomography was also used to begin to detect process-induced flaws for subsequent comparison to metallographic and fractographic examinations in both ASTM standard samples as well as parts.
Figure 1 shows some of the process-induced features (i.e. lack of fusion – LoF) SEM-imaged on fracture-tested samples that can affect the mechanical performance in addition to imparting mechanical anisotropy, while Figure 2 shows non-destructive tomographic images highlighted to illustrate process-induced defects prior to fracture testing. The SEM image in Figure 3 illustrates the surface roughness (i.e. unmelted powder + isolated surface roughness/cracks) that is typically present on as-deposited surfaces (i.e. external and internal). The effects of these features along with process-induced microstructural changes on the mechanical reliability continue to be investigated by the AMMRC and the rest of the community.
Figure 1. Fracture surface SEM images of Ti-6Al-4V sample prepared by additive manufacturing that illustrates multiple lack of fusion (LoF) features at various locations [reference - JOM, 67(3), 597–607 (2015)] in a horizontal build. Crack growth direction is top to bottom in the image.
Figure 2. Computerized tomographic image showing sub-surface process-induced flaws in early AM-processed vertical build of Ti-6Al-4V. Sample dimensions: 10mm x 20mm x 100mm. [reference - JOM, 68(3), 747-764 (2016)].
Figure 3. SEM image of as-deposited surface of AM-processed Ti-6Al-4V. Partially melted powders and other features (i.e. surface roughness, cracks) are evident at various locations. [reference - JOM, 67(3), 597–607 (2015)].
We invite you to join us in the AMMRC’s 35th anniversary celebration as we celebrate decades of research, development, and Center milestones. Visit the AMMRC web site, ammrc.case.edu, and keep watch on social medial for insights on the AMMRC through the decades as we share stories about the evolving laboratory and honor the efforts of the diverse academics, staff, and students that have propelled the AMMRC forward.
Social media: Join us on social media for fun and engaging content that will help you discover the AMMRC’s history and where it’s heading in the future. #AMMRC35.