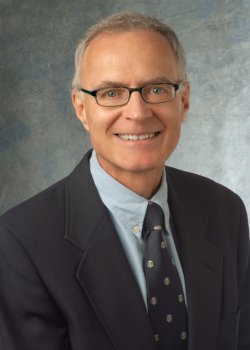
AMMRC Celebrates 35 years of Mechanical Characterization at CWRU
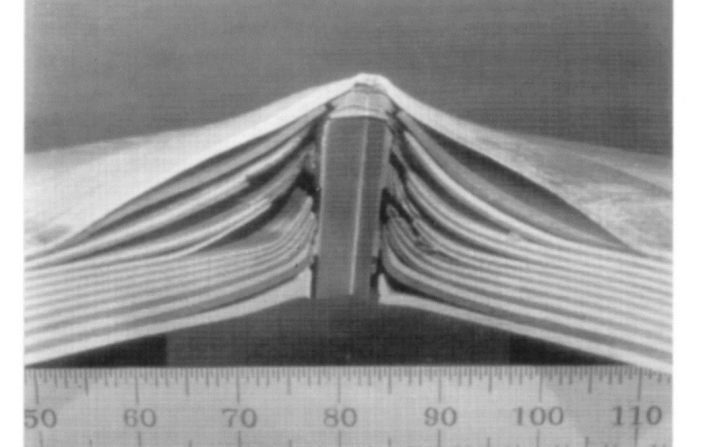
The years 1995-2000 continued work from the early 1990’s with additional funding exceeding $3M, along with continued growth of the AMMRC manufacturing facilities and Lewandowski research group to include: Ajay Vaidya (M.S.), John Short (M.S.), Anand Samant (M.S.), Craig Robinson (M.S.), Lorie Ludrosky (M.S.), Jim McCrindle (M.S.), Bill Zinsser (M.S.), Pat Dickerson (M.S.), Jose Oviedo (M.S.), Gautham Ramachandran (M.S.), Karthik Subramanian (M.S.), John Carrigan (M.S.), Lisa Yost Ellis (Ph.D.), Todd Osman (Ph.D.), Cheryl Cullers Bowman (Ph.D.), Erik Hilinski (Ph.D.), Peravudh Lowhaphandu (M.S./Ph.D./Postdoc), Dr. S. Wen, Dr. Joe Rigney.
Multiple new individual multi-year research grants were obtained from ALCOA, MTS Systems Corporation, General Electric, Howmet, Luxfer USA, Air Force Office of Scientific Research (AFOSR), Office of Naval Research (ONR), NASA Glenn Research Center, NASA HQ, National Science Foundation (NSF). In addition, major equipment funds were obtained from the NSF-Materials Research Infrastructure (MRI) program, leveraged with funds from the Ohio Board of Regents (OBR), ALCOA, and Timken to design and purchase Advanced Deformation Processing equipment from MTS Systems. This large-scale equipment included a multi-actuator Forging Simulator for bulk forging simulations, Figure 1, along with a Forming Simulator, Figure 2, for sheet metal forming. In addition to continuing research with various other universities, companies, and government labs that started in the 1990’s, exciting work continued on laminated metal composites, niobium-silicon alloy in-situ composites, bulk metallic glasses, as well as initiating manufacturing research using the deformation processing simulators shown in Figures 1 and 2.
A selection of highly cited papers from 1995-2000 that emerged from his research group and collaborations with Lawrence Livermore National Lab, Stanford, ALCOA, General Dynamics, and Boeing included work on laminated metal-matrix composites that were being considered for lightweight armor and jet engine containment applications due to their exceptional damage tolerance as shown in Figure 3 and explained in the major review, "Mechanical behaviour of laminated metal composites". Work on high temperature intermetallics under consideration for a number of aero-engine applications included: "Loading rate and test temperature effects on fracture of in-situ niobium silicide-niobium composites" and "Refractory metal-intermetallic in-situ composites for aircraft engines". Work on bulk metallic glasses documented their surprising high damage tolerance/toughness, "Fracture toughness and notched toughness of bulk amorphous alloy: Zr-Ti-Ni-Cu-Be". Another major review article, "Effects of hydrostatic pressure on mechanical behaviour and deformation processing of materials” captured the effects of superimposed pressure on mechanical behavior and deformation processing, while "Effects of superimposed hydrostatic pressure on flow and fracture of a Zr-Ti-Ni-Cu-Be bulk amorphous alloy” was the first to detail these effects on bulk metallic glasses. The fatigue behavior of lightweight magnesium composites manufactured in the Case Metal Processing Lab was highlighted in the "Effects of SiCp size and volume fraction on the high cycle fatigue behavior of AZ91D magnesium alloy composites”.
The collaborative work on laminated metal matrix composites demonstrated high damage tolerance and resistance to penetration as illustrated in Figure 3. The 1988 review article highlighted the Nobel Prize work of Percy W. Bridgman on pressure effects on materials and summarized the more recent work around the world and at CWRU on a variety of structural materials, in addition to bulk metallic glasses, that demonstrated the increased formability possible with such approaches. The early work on refractory metal intermetallic in-situ composites for aircraft engines has provided a basis for more recent work at CWRU and elsewhere in the 2020’s.
We invite you to join us in the AMMRC’s 35th anniversary celebration as we celebrate decades of research, development, and Center milestones. Visit the AMMRC web site, ammrc.case.edu, and keep watch on social medial for insights on the AMMRC through the decades as we share stories about the evolving laboratory and honor the efforts of the diverse academics, staff, and students that have propelled the AMMRC forward.
Figure 1. Multi-actuator Advanced Forging Simulator capable of single- or multiple-sequence forging simulations on sub-scale billets emulating industrial forgings.
Figure 2. Advanced Forming Simulator for novel sheet metal forming experimentation. Conventional die sets enable the construction of forming limit diagrams while custom die sets enable sub-scale sheet metal forming of more complicated shapes.
Figure 3. Laminated metal composite demonstrating high damage tolerance and defeat of projectile. Photo courtesy of International Materials Reviews, "Mechanical behaviour of laminated metal composites".
Social media: Join us on social media for fun and engaging content that will help you discover the AMMRC’s history and where it’s heading in the future. #AMMRC35.