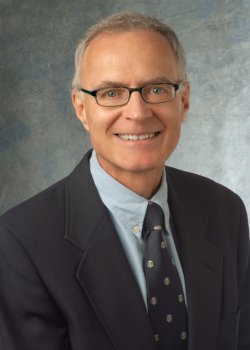
AMMRC Celebrates 35 years of Mechanical Characterization at CWRU
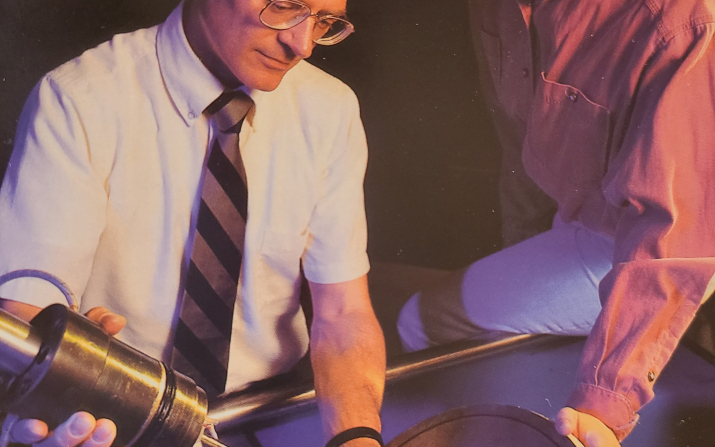
The years 1990-95 built on the initial progress made in the late 1980’s with increased research and equipment funds exceeding $3.2M, along with expansion of the Lewandowski research group that included: Dave Miller (M.S.), Mark Assel (M.S.), Jennifer Wolfe (M.S.), John Frank (M.S.), Frank Ritzert (M.S.), A Lavonne Grow (M.S.), Janice Walkup (M.S.), Yousef Esmaelipour (M.S.), Ajay Vaidya (M.S.), Peravudh Lowhaphandu (M.S.), John Short (M.S.), Anand Samant (M.S.), Craig Robinson (M.S.), Stuart Maloy (M.S./Ph.D.), Lisa Yost Ellis (M.S./Ph.D.), Todd Osman (M.S./Ph.D.), Gary Rozak (Ph.D.), Jan Kajuch (Ph.D.), Erik Hilinski (Ph.D.), Joe Rigney (M.S./Ph.D./Postdoc), Robert Margevicius (Ph.D./Postdoc), Chanqi Liu (Ph.D./Postdoc), Dr. Preet Singh, Dr. John Zhang, Dr. David Schwam, and Dr. Sunil Patankar.
Multiple new individual multi-year research grants were obtained from ALCOA, MTS Systems Corporation, Air Force Office of Scientific Research (AFOSR), NASA Lewis Research Center, NASA HQ, National Science Foundation (NSF), Defense Advanced Research Projects Agency (DARPA), and the DARPA equipment grant to build a unique high pressure testing apparatus in collaboration with Lawrence Livermore National Lab (LLNL) shown in Figure 1. In addition to continuing research with various other universities, companies, and government labs that started in the late 1980’s, exciting work began on first generation aluminum-lithium alloys, laminated metal composites, molybdenum disilicide, niobium-silicon in-situ composites, as well as high pressure effects on both processing and properties of metal matrix composites and intermetallics.
A selection of highly cited papers from 1990-95 that emerged from his research group and collaborations included work on metal-matrix composites that have been used in a variety of automotive (e.g. brake drums, drive shafts), aerospace (helicopter rotor, F-16 ventral fins and fuel access covers), and sports/fitness (bicycle frames) applications: "Crack initiation and growth toughness of an aluminum metal-matrix composite", "Segregation to SiC/Al interfaces in Al based metal matrix composites”, “Observations on the effects of particulate size and superposed pressure on deformation of metal matrix composites”, and “Effects of heat treatment and reinforcement size on reinforcement fracture during tension testing of a SiCp discontinuously reinforced Al alloy”. Work on high temperature intermetallics under consideration for a number of aero-engine applications included: "Strength and ductile-phase toughening in the two-phase Nb/Nb5Si3 alloys”, “Deformation and fracture behavior of Nb in Nb5Si3/Nb laminates and its effect on laminate toughness”, and “Carbon Additions to Molybdenum Disilicide: Improved High-Temperature Mechanical Properties”.
The work on metal matrix composites utilized in-situ observations conducted during mechanical testing in addition to testing samples with superimposed pressures exceeding 1 GPa (over 150,000 pounds/square inch!). The high-pressure work revealed the beneficial effects of superposed pressure on extending the ductility and formability of these materials, relevant to the deformation processing of these materials into shapes. The work on intermetallics showed that significant increases in fracture toughness of nominally brittle materials could be realized via various alloying approaches combined with microstructure design.
We invite you to join us in the AMMRC’s 35th anniversary celebration as we celebrate decades of research, development, and Center milestones. Visit the AMMRC web site and keep watch on social medial for insights on the AMMRC through the decades as we share stories about the evolving laboratory and honor the efforts of the diverse academics, staff, and students that have propelled the AMMRC forward.
Figure 1. Professor John Lewandowski and graduate student Lorie Ludrosky prepare a sample for high pressure testing in the DARPA-funded and LLNL-designed high-pressure testing apparatus. The fundamental flow and fracture behavior of various composites (Al, Mg), intermetallics (NiAl, Ni3Al), monolithic metallic alloys (Ti, Al, Mg, Fe), and metallic glasses were explored with this novel equipment. Photo courtesy of CWRU Annual Report 1991.
Social media: Join us on social media for fun and engaging content that will help you discover the AMMRC’s history and where it’s heading in the future. #AMMRC35.
###